What Is HSS Twist Drill Bit?
HSS twist drill is a type of drilling tool made of High-speed steel used for metal processing. HSS is a special alloy steel with excellent abrasion resistance, thermal stability, and cutting properties, making it ideal for metalworking tasks such as drilling. A twist drill (also known as auger or spiral flute drill) is a drill with helical flutes that allow cutting chips to exit the drill hole quickly, reducing friction and heat during drilling and improving drilling efficiency. The design of HSS twist drills makes them suitable for a wide range of different metal materials, including steel, aluminum, copper and alloys, etc. as well as wood type machining.
Characteristics Of High-Speed Steel Twist Drills
1. High Abrasion Resistance: High-speed steel materials exhibit excellent abrasion resistance, allowing the cutting edges to stay sharp for extended periods.
2. High Heat Stability: High-speed steel can operate in high-temperature environments without significant loss of hardness or deformation.
3. Excellent Cutting Performance: The spiral groove design of twist drills contributes to effective metal cutting while reducing chip accumulation.
4. Reliable Machining Quality: High-speed steel twist drills typically deliver high-quality drilled holes with precise dimensions and smooth surfaces.
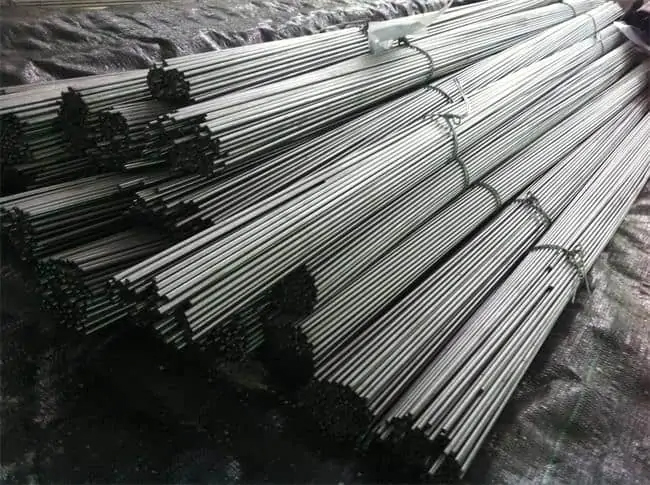
HSS Types We Used For Our Twist Drills
The main grades of HSS we use are: M42, M35, M2, 4341, 4241.
There are some differences between them, mainly related to their chemical composition, hardness, thermal stability and areas of application. Below are the main differences between these HSS grades:
1. M42 HSS:
M42 contains 7%-8% cobalt (Co), 8% molybdenum(Mo) and other alloys. This gives it better abrasion resistance and thermal stability. M42 usually has higher hardness, and its rockwell hardness is 67.5-70(HRC) which can be achieved by heat treatment techniques.
2. M35 HSS:
M35 contains 4.5%-5% cobalt and also has great abrasion resistance and thermal stability. M35 is slightly harder than normal HSS and usually maintains a hardness of betweeb 64.5 and 67.59(HRC). M35 is suitable for cutting sticky materials such as stainless steel.
3. M2 HSS:
M2 contains high levels of tungsten (W) and molybdenum (Mo) and has good cutting properties. The hardness of M2 is usually in the range of 63.5-67(HRC), and it is suitable for the machining of metals that need higher requirements.
4. 4341 HSS:
4341 HSS is a high speed steel with a slightly lower alloy content relative to m2. The hardness is generally maintained above 63 HRC and is suitable for general metal working tasks.
5. 4241 HSS:
4241 HSS is also a low alloy HSS containing less alloying elements. The hardness is generally maintained around 59-63 HRC and is usually used for general metal working and drilling.
Choosing the proper grade of HSS depends on your specific application needs and the type of material to be processed. Hardness, abrasion resistance and thermal stability are the key factors in the selection.
Post time: Sep-18-2023